Sand Casting
Material focus
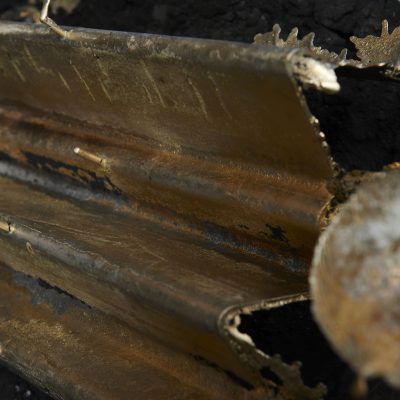
The knowledge and manual skills of Henge’s craftsmen make this process an element of masterful customization, achieving shapes and thicknesses that go beyond design limits.
In its efforts to continue research and rework techniques that have been part of the Italian craftsmanship tradition for centuries, Henge has intertwined its ideas and products with a type of fusion grounded in nature and its elements: sand casting.
Sand casting is a process that uses unique and nonreusable sand molds that hold molten metal. It consists of four basic steps: assembling the sand mold, filling the mold with liquid metal, cooling the metal, and removing the sand and casting. The process may seem simple, but it encounters many obstacles that can compromise the successful creation of the product.
A technique with a long tradition that finds a new vocation for uniqueness and creativity with Henge.
This perfected sand casting technique is one of the few capable of supporting metals that melt at high temperatures, such as nickel and titanium. It is a process that combines Henge’s philosophy of creating unique pieces thanks to its incredible flexibility and ability to address the factors that make the final result special. The characteristics of the sand and its use greatly affect the product and become an instrument for customization and creativity.
Many properties of molding sand depend on the size of its grains and the distribution of the sand. The force, or the ability to maintain the shape of the mold even under strong mechanical stress, along with the sand mold’s permeability, or the ability of the sand to penetrate and flow through the smallest cavities of the detailed parts, are all characteristics that Henge bends in order to achieve exceptional results. The Saetta Table, designed by Massimo Castagna, has a fine and elegant structure that combines the stone top with the brass and bronze sand casting legs with striking linear details. Thanks to their folded design, Massimo Castagna’s sand casting brass mullions of the Be-Mine Coffee Tables become a trait-d’union from the base to the top in the shiny brass, creating light and shadow effects. The Mushroom Tables, exclusive Yabu Pushelberg Studio creations, are made of sand casting brass and bronze and are characterized by their great communicative power and their ability to fully express the uniqueness of this process. The Henge customization experience pushes this technique to its peak, beyond dimensional and formal limits. By experimenting with new effects and expressions that make sand casting completely unique and by inserting it as part of a vast array of elements and production techniques, Henge’s possibilities of combinations become infinite.
In its efforts to continue research and rework techniques that have been part of the Italian craftsmanship tradition for centuries, Henge has intertwined its ideas and products with a type of fusion grounded in nature and its elements: sand casting.
Sand casting is a process that uses unique and nonreusable sand molds that hold molten metal. It consists of four basic steps: assembling the sand mold, filling the mold with liquid metal, cooling the metal, and removing the sand and casting. The process may seem simple, but it encounters many obstacles that can compromise the successful creation of the product.